Crash87
Active member
Team - if you saw my thread over on backpack hunting it was about getting suggestions for gear after my whole rig was ripped off on the way home from Colorado last fall. In there I relayed I was building a rifle to replace the ones stolen and was asked to post a thread on it. I will try over the course of this to relay what I do to build rifles and get them shooting well.
For this build I went with a Remington 700 Long Action Magnum receiver for the 338 Win Mag cartridge. Scope is a Vortex Viper PST. Stock is a Hogue full bedded varmint version. Timney trigger and a Shilen select match Sendero contour. Apologies for the messy bench! More to follow.
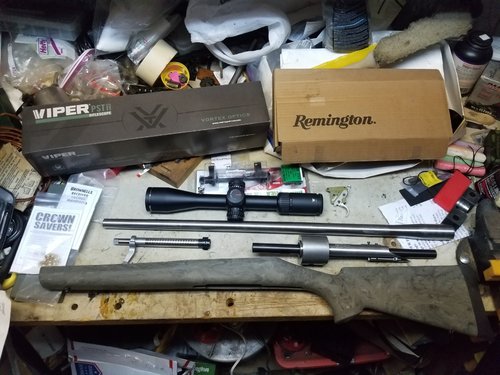
For this build I went with a Remington 700 Long Action Magnum receiver for the 338 Win Mag cartridge. Scope is a Vortex Viper PST. Stock is a Hogue full bedded varmint version. Timney trigger and a Shilen select match Sendero contour. Apologies for the messy bench! More to follow.
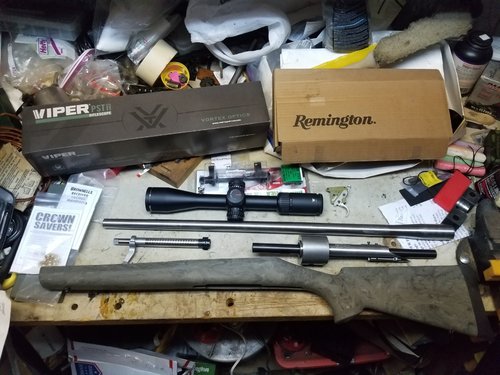